Week 13: Project Summary
- Mao Polosky
- May 30, 2024
- 7 min read
Setting a Foundation: Getting Started in Summer 2023
I've been working on environmental projects since middle school. The typical student volunteer things? I've done them all. I've taught recycling to my neighborhood, hosted waste-to-art contests at schools, made posters and taught summer classes. On the science side, I joined ASDRP Research just wanting to do something related to the environment, and found myself joining a group based on doing research on cement replacements in concrete without any prior knowledge. I learned a lot about the basics of cement and concrete, but the fact that the concrete industry is very old and therefore has very specific test standards meant we didn't have the equipment needed to do thorough SCM testing. Therefore, I took matters into my own hands the summer of 2023, cold-calling/emailing various professors and companies to see who could help me. The result? Nothing...
Nothing until, as a last ditch effort, we stopped by the local office of Cemex, an international concrete company, asking if they could help. They put us in contact with Nick Barnett, who expressed interest in passing down the baton of concrete knowledge to the next generation, and put me in contact with Eric, who runs a Cemex concrete lab in Livermore, CA. With that set, I sought out new SCMs that had not been heavily studied, but that were still available in the bulk amounts required for industrial testing at Cemex. We browed Amazon, Ebay, Home Depot, eventually getting to Chinese websites which sold a reasonable amount of material for a lower price (although 50kg of SCM was still over $1000 with shipping). Thanks to my mom and a family friend visiting China at the time, we were able to negotiate a purchase of Coconut Shell Ash (CSA).

Naively, bringing the CSA to Cemex, I imagined good results, quick and easy. I would become a concrete champion. Unfortunately, the strength turned out weak, the concrete splitting around the aggregates, showing that even the rocks were stronger than my CSA concrete. I was discouraged, thinking all my work was wasted just because success wasn't achieved immediately.
Later in the year in Industrial Chemistry, I was once again stirred to action. We were watching a documentary on why recycling, although scientifically sound, was actually ana incomplete solution to plastic waste as it was just not economically viable (mostly). Seeing this (and also writing all my college essays on "interdisciplinary" solutions), I realized that environmental issues needed to be analyzed from all points of view, scientific, mathematical, social and economical. Connecting the dots, I saw that the concrete I had almost abandoned could be made more sustainable only by considering all these angles, since it's integrated into our societies just as much as plastic waste. The challenge of this new view, but also the potential benefits for humanity brought me back to the drawing board.
Drafting a Foolproof Plan
First of all, we had to fix the issue from the previous part of the project. For this, we planned on burning off the excess carbon that doesn't contribute to concrete strength, leaving more "pozzolanic" chemicals such a SiO2 (silica) and Al2O3 (alumina) and "cementitious" ones such as CaO (calcium oxide) which do contribute to strength. We would then repeat industrial testing at the Cemex lab and compare.
On top of that, considering what I had learned about interdisciplinary approaches, I decided I would do lots of literature review, not just on CSA, but on other SCMs as well, looking at how they fit together and within the wider world. The goal was to evaluate CSA's viability from all angles. Another benefit of this is that it would not only fill the time taken by the concrete curing, but its success would also not depend on the CSA itself, we had proved to be difficult to work with.
Lastly, I wanted to see if there were other ways in which CSA may be chemically/physically altered to be more effective. I didn't know how I would do this at the time, but I would figure that out later (famous last words).
Burning Questions
As I presented my plan at the senior project proposal, I was scared it was a bit too simple, and I'd have tons of extra time to sit around. Fortunately or unfortunately, experiments always take way more time than you expect (as Dr. B has said before).
Most of the project except the literature analysis hinged on the kiln-burning of the CSA to remove excess carbon. This is where my first challenge lay. It turns out although Nick at Fortera had containers that could withstand 900 C temperatures, these were small ceramic crucibles that held just grams of material at a time. At this rate, the burning of 25-30kg of CSA would take months. The issue was that the Cemex industrial tests had to start early so we could get 28-day test results before senior project was over. So, it was up to me and dad again to solve this problem.
We first looked online, but only found small containers, too-weak-containers and very very expensive containers. We decided to take to the road, visiting a local pottery store, Clay Planet, to see if they had advice/containers big and strong enough. There, a pottery professional gave us a few pointers on containers we could go find/custom-make, but had nothing suitable for us. Still, he raised the point that CSA could also be used as a glaze, as other plant ashes (wood ash, rice ash, etc.) had been used for this in the past. Although unsuccessful here, we gained new insight for potential uses of CSA (mostly a waste material). Finally, after a week or two, my dad remembered a website that sells all kinds of industrial-use items, and they happened to have strong type-304 stainless steel containers of reasonable size for sale. The project had barely begun and we were having fun!

(Various bowls made with natural plant ash as a glaze. Glazes are composed of silica, alumina and "flux", which is materials added to lower melting temperature of the glaze)
We brought the containers and CSA to Nick, who graciously burned it for us. The burned ash in the steel containers is shown below. Apparently, the CSA was so messy to work with that Nick had to cover all the work surfaces with towels. Sorry about that!
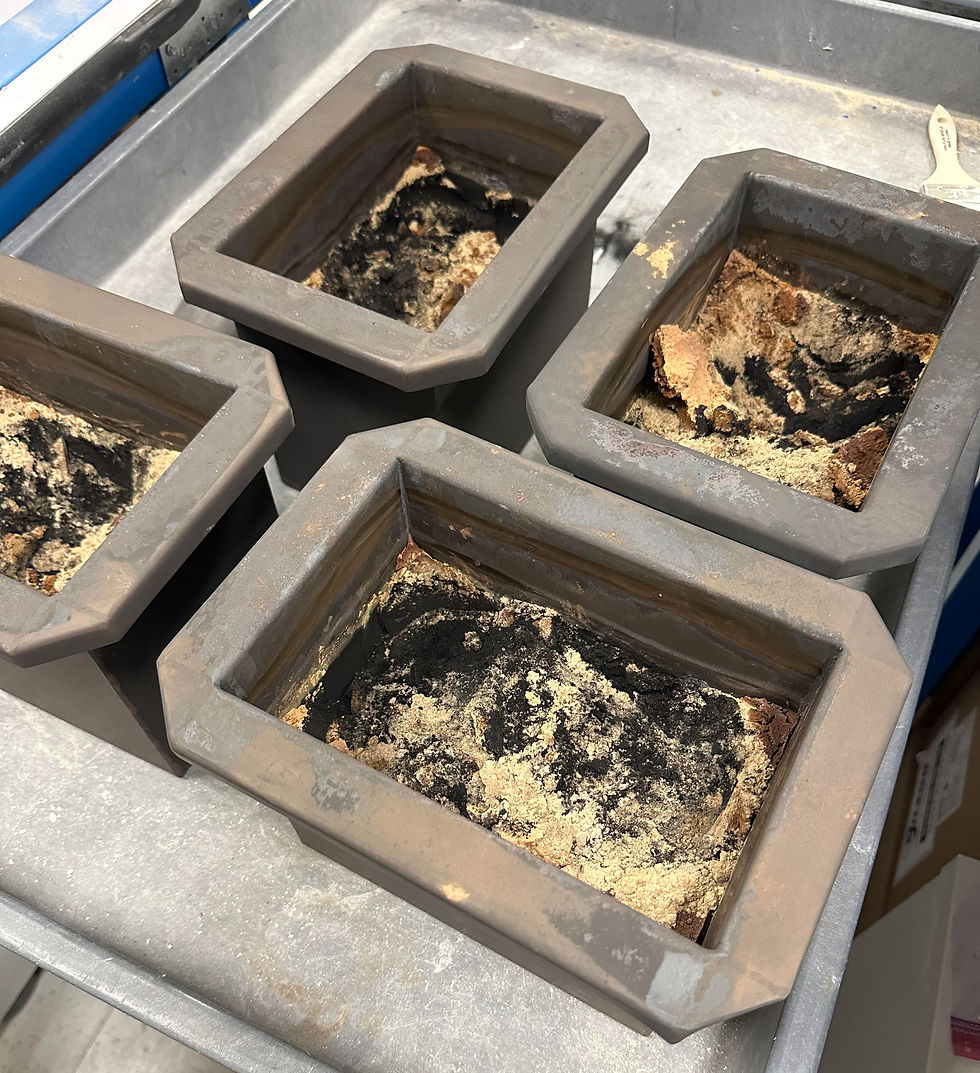
(Burned CSA in the 4 "304" stainless steel containers we bought)
Industrial Testing Time
Time passed quickly. While I researched the supplies of common and new SCMs, along with their emissions, geography, and other sustainability factors, it was almost mid-March. The report from Nick? The CSA was still burning at a slow rate of around 3-8kg of final material per week. There was no way we were going to get the full 25-30kg of burned material in time for the date set by Cemex. A compromise had to be made. Last time, we replaced cement with CSA at 15, 25 and 35%. This time, we lowered the amounts to 10, 15, and 25%. The 15% could still be compared with the previous times, and a lower replacement is more realistic for most plant-based SCMs anyway. I made this proposition to Eric at Cemex, and we went through with the plan.

(Cemex Lab in Livermore)

(Concrete Cylinders and Shrinkage molds at Cemex lab)
Acid-Treatment, Small Cubes
As I worked on my literature analysis, I also formulated plans for more experimental tests in the BISV lab. Through reading papers, I found that with acid solutions, the effectiveness of pozzolans (i.e. the alumina/silica in CSA) could be increased. I also knew from my ASDRP days that geopolymer concrete, made with 100% SCMs and 0% cement, could be made using a highly alkaline (basic) solution such as 14M NaOH. Although we didn't have much equipment at school, we thankfully had spare silicone ice cube trays, and Dr. B somehow just had a plastic spoon and sharpie in her lab coat that I needed. I was going to use the sand at school, but it was unlabeled Nick recommended to buy some standard "Quikrete" sand at a Home Depot/Lowe's instead. I also had a 50lb bag of standard Type II/V cement laying around. I hauled these over 100 pounds of items up to the 3rd floor and began work.
Getting Results
Mysteriously, according to the industrial tests, the new, kiln-burned CSA concrete was somehow weaker than the original concrete. We did chemical analysis at Fortera, and found that carbon content in CSA had gone down (though not as much as we wanted), so this result doesn't make much sense as of yet. The rust caused during the summer tests on the steel shrinkage molds was also seen again.

(Rust seen on the shrinkage molds 1 day after mixing of concrete and putting into molds)
On the acid side, I brought the final batch of cubes to Fortera for compressive strength testing the day before the final presentations (talk about cutting it close). It does seem that the concrete cubes with acid-treated CSA (0.1 and 1.0M concentrations of both HCl and acetic acid) performed better than the non-acid controls, but due to the hand-mixed methodology of the experiment, variation between cubes was significant, and so no definite conclusion can be drawn currently.
Finally, about the literature interdisciplinary analysis. CSA seems to have potential to add more SCM supply as SCM demand grows (although CSA supply is relatively smaller). Another point for CSA is that it's grown in Southeast Asia (mainly Philippines, Indonesia, India) where lots of infrastructure development is expected to happen. Also, CSA could have economic and political benefits for these countries as well. Still, due to a lack of bulk reliable data for things such as supplies of SCMs and the emissions they cause. There is clearly a need for standardization in this regard so that companies and policymakers can have more reliable (or "concrete") information to make decisions with. Overall, it's looking okay for CSA here.
Conclusions
There are still many questions floating around, so I wouldn't say the work here is over. That's just how science works sometimes; scientists spend years studying a single thing, with countless failures along the way. That's just how it is. What really matters to me is that I'm working on something meaningful, gaining tons of industry experience along the way. I loved every challenge and all the new people I met and new experiences I had through them.
As opposed to how I felt after the first phase of the project "failed", this new "failure" has motivated me to use my expanded resources in college to continue answering the questions essential to finding equitable and interdisciplinary solutions to environmental issues that are actually feasible.
Thank you so much for following my journey!
I'll see you all around.
Max Polosky
Comments