A Week in Review: Week 10, Coconut & Acid Concrete Pt. 2 and Basic Troubles
- Mao Polosky
- May 5, 2024
- 4 min read
Can you spot my assistant Sidhant?
Hello once again, my reader(s), this week was a crucial one, as we:
Finally finished processing the Acid-treated Coconut Shell Ash (CSA) enough to use it to make concrete (10% replacement of cement with the treated CSA).
Finally figured out how to dissolve enough solid NaOH in water to make 16 molar (highly concentrated NaOH solution for pozzolanic activity test of the CSA.
Started considering plans for finishing up my end product(s) in the next weeks.
So let's get right into it!
Acid-Activated Coconut Shell Ash Concrete Mixes
Step 1: Mixing the Ash and the Acids
First, I picked two different acids to use as experimental groups to compare to the regular non-CSA concrete and unprocessed 10% CSA concrete. I picked HCl as my strong acid and acetic acid as my weak one, both of which were also used in my referenced literature. Then, I chose to use a 0.1 molar and 1.0 molar concentration of each acid, therefore creating 4 experimental groups, comparing the effects of both strong/weak acid and acid concentration.
Supposedly, the acids can enhance the pozzolanic effects of Supplementary Cementitious Materials (SCMs i.e. cement replacements), thus making the resulting concrete stronger than if unprocessed material was used.
After creating the acidic solutions in beakers, I added in the CSA and magnetically stirred the mixtures for 24 hours. The purpose was to create as much contact between the CSA and acid solutions as possible. Some properties of the CSA I observed, such as the lightness and oiliness of certain particles within the ash made the mixing process difficult, so this could effect results.
After 24hrs of mixing, I let the CSA settle for 72 hours.
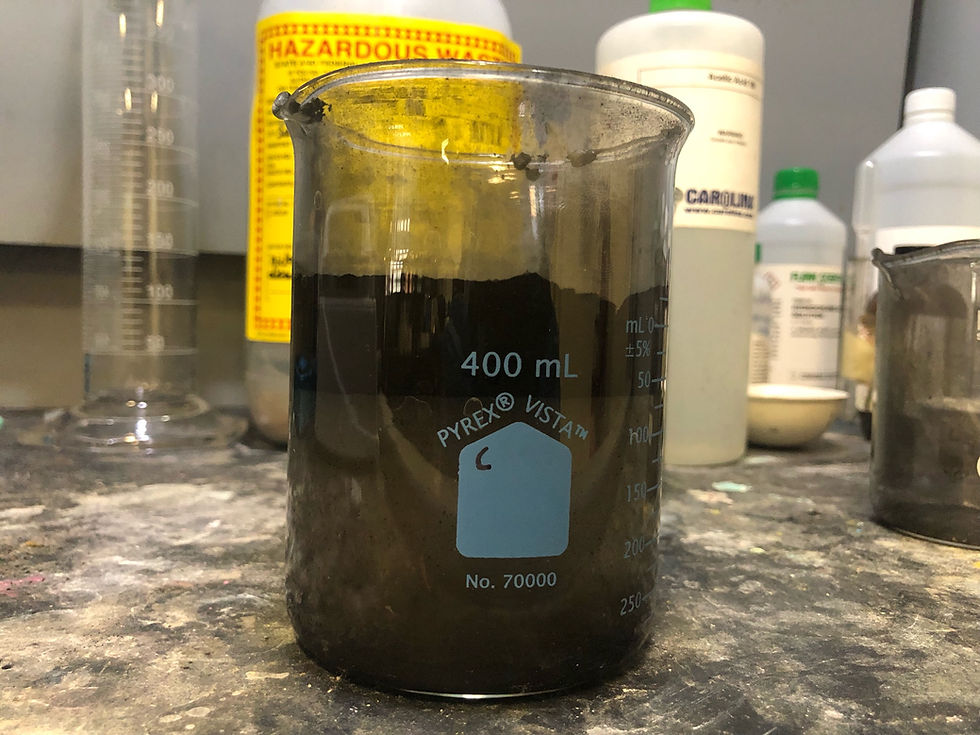
(The Coconut Shell Ash can be seen floating above the acid solution initially)
Step 2: Filtration, Re-Ashification
After settling, the literature centrifuged the solutions to separate out the ash again, but we didn't have those capabilities at school, so we used the good old gravity filter method instead. With a simple setup of a funnel with filter paper inside, the filtrate passes through while the original filtride remains.
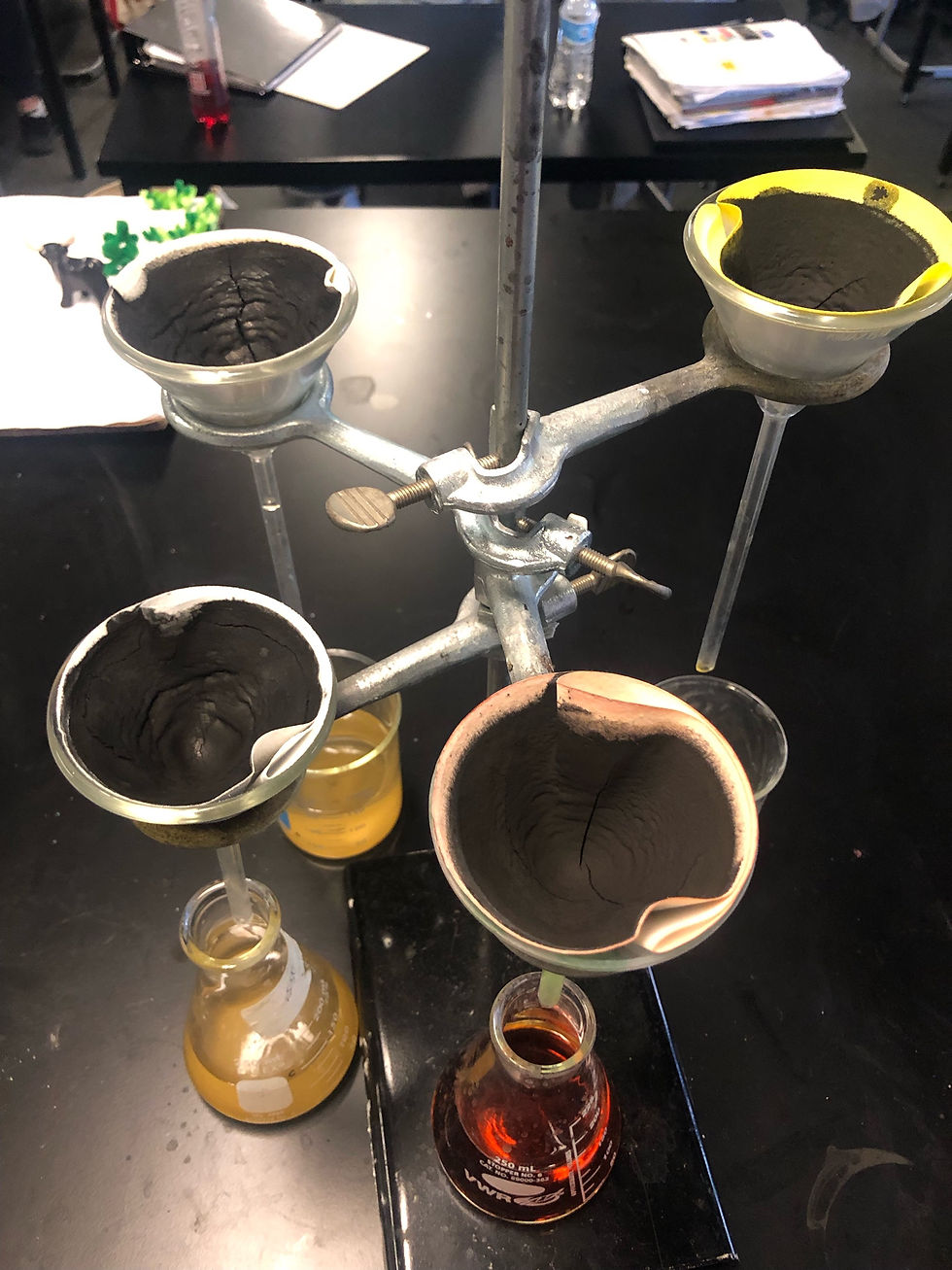
(CSA layer caked on the filter papers)
Unfortunately, the ash was so fine that it created a clay-like layer on the filter paper, slowing the filtration process. It took 2 days to finish filtering all of the CSA back out. Then, weighing our yields of ash after filtration, we found that the weight was significantly higher than the initial 20g CSA put into the solutions. So, we put the desiccator in the chemical room into use for 24 hours to try and evaporate some of the remaining solution, reducing the weight closer to the original 20g.
One interesting note with the filtration was a fine layer of solid (precipitate) on the bottoms of filtrates A and C (the 0.1M solutions of HCl and acetic acid, respectively) but not the 1.0M solutions). Chemical analysis in the future may reveal more information on the reason(s) for this. Who knows, it may be an interesting breakthrough.
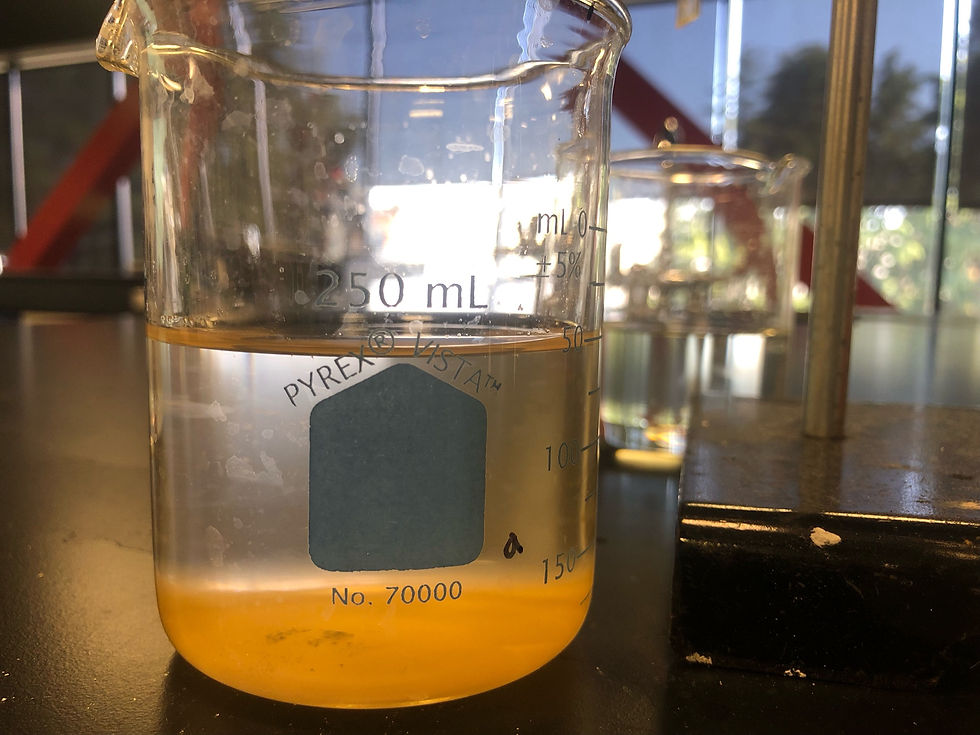



Part 3: Finally Time for Concrete
After all of that, it's Thursday and finally time to make concrete. The concrete needs two weeks to mature before crush testing, the results should be out a day before final presentations. Talk about cutting it close.
With help from my other trusty assistant, Kevin, we quicky made 4 batches of concrete and poured them into the cube molds to harden.

(Processed ash (looks identical to non-treated CSA))
Creating a Concentrated Alkaline Solution
Another test I wanted to perform was a pozzolanic activity test, which uses a concentrated 16M alkaline solution (as we discussed last week). Our first attempt ended in non-dissolution. This time, we calculated the exact volume of water necessary (using NaOH density values) and added the solid NaOH chips in small portions while stirring magnetically. The resulting solution is a bit cloudy but definitely more dissolved than the first attempt.
To Summarize Everything...
The acid treatment of CSA has yielded various unexpected and difficult results. These have been frustrating in terms of time constraints but intriguing in terms of the science behind the results, which will be further investigated in the near future. I also hope to travel to Cemex to get compressive strength and chemical composition results in 1-2 weeks for the cubes to make more conclusions.
As we near the end of our project, it's also sadly important to consider where to stop and how to communicate the work to the public. I already have a paper written based off my previous year of work on the project, so adding the new work to that should be relatively simple. But, I want to really engage with the masses, so I'm thinking of writing a shorter magazine-style article in hopes of really attracting more interest in the important topic of sustainable concrete and construction.
Thanks for getting this far! I'll see you all next week.
Max Polosky
Coconut Fact #6: "The coconut palm bears fruit for 15 to 60 years. In ideal conditions, fruit production lasts for up to 80 years and the maximum age of the coconut palm is between 100 and 120 years." - https://timesofindia.indiatimes.com/life-style/food-news/world-coconut-day-interesting-facts-about-coconut-that-you-need-to-know/photostory/85859171.cms?picid=85859228.
Comentários