A Week in Review: Week 9, Lab-Grown Coconut and Acid Concrete
- Mao Polosky
- Apr 29, 2024
- 3 min read
Updated: Apr 30, 2024
(Can you spot my assistant Sidhant?)
Hello readers! It's been an eventful week, let's get right into what I did this week in the lab:
Acquiring the materials for my concrete (running around to various locations).
Creating miniature concrete cubes in the chemistry lab with acid and alkaline-treated Coconut Shell Ash (CSA) concrete.
Now that's only one thing, but lab work always ends up requiring much more time than expected.
Lab-Grown Concrete
Materials Gathering
Making concrete is just like baking a cake: you need the ingredients or you can't make the cake. Unfortunately, a week before the lab work had to begin, my ingredients were not present. I set up a shopping list (Type II/V cement (common type of cement in California), some burnt Coconut Shell Ash (CSA), sand, water, and ice cube trays as molds).

(Coconut Shell Ash in bucket, from Cemex)
First was the burnt CSA, which Nick burned for me at Fortera. On Wednesday, I drove 30 minutes up to Fortera and back to get the CSA, careful to secure the lid so the fine powder wouldn't coat the inside of my car.
Next was the cement. I had a bag of Basalite Type II-V Cement in storage from past work at ASDRP Research, so I just grabbed that.
I was going to use the sand from Industrial Chemistry at school, but Nick told me a standardized sand was better so we got Quikrete All-Purpose Sand from Home Depot instead.
At school, I found some silicone trays similar to the ones I used in Industrial Chemistry.
Making the Concrete(s)
Thursday
So, down to business. With my lab assistant Sidhant, I first made 6 control cubes with a standard 1:2:4 water:cement:aggregate ratio, using only sand since the small size of the cubes meant gravel aggregates would be impractical. Then, I replaced 10 and 20% of the cement with CSA, 3 cubes each for 6 more cubes. Unfortunately, the school didn't have any distilled water left, so I drove to Safeway to get two bottle in the middle of experimentation.
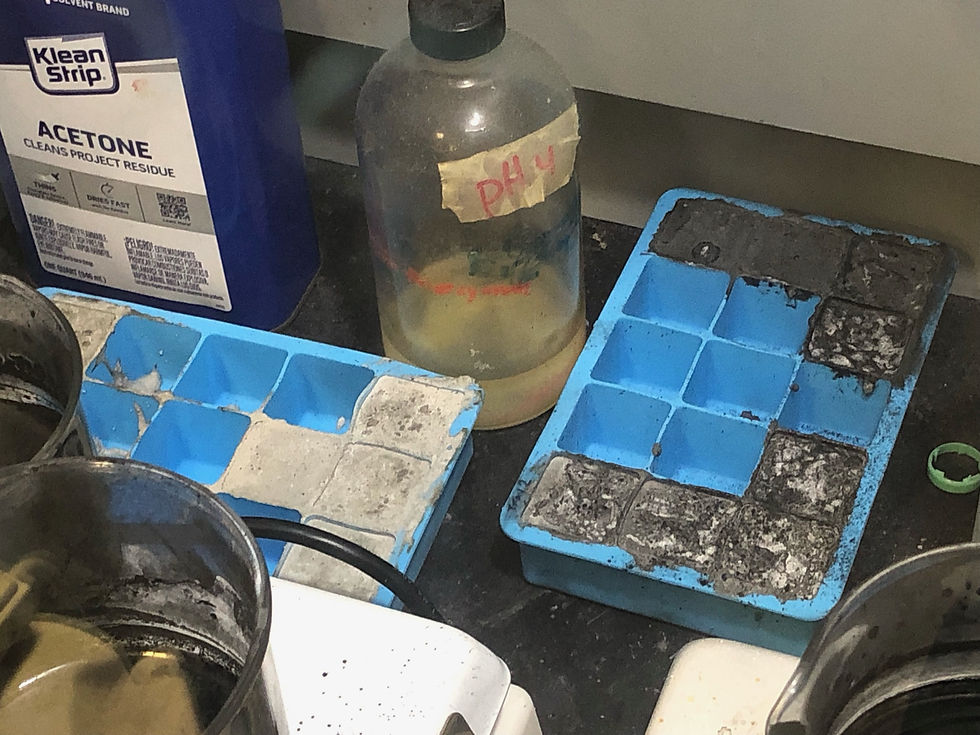
(control (left) and CSA concrete (right) in the fume hood)
Next was the harder experimental part.
First, the acid treatment for the CSA, which is supposed to bring out the pozzolanic (strength-giving) properties of Supplementary Cementitious Materials (SCMs). I used 0.1M and 1.0M concentrations of Hydrochloric Acid and Acetic Acid, then put in CSA in a 1:15 CSA to solution ratio. I then left them stirring for 24 hours to react with the solutions, then leaving them to settle over the weekend. Today, I gravity-filtered the solutions to separate the ash back out, which had developed deposits of green and white solid, possibly iron (can be green) or other ash material. If ash can be separated out from the mostly carbon CSA without burning, this could make using CSA even more sustainable. I will try to make concrete with the acid-activated ash soon.
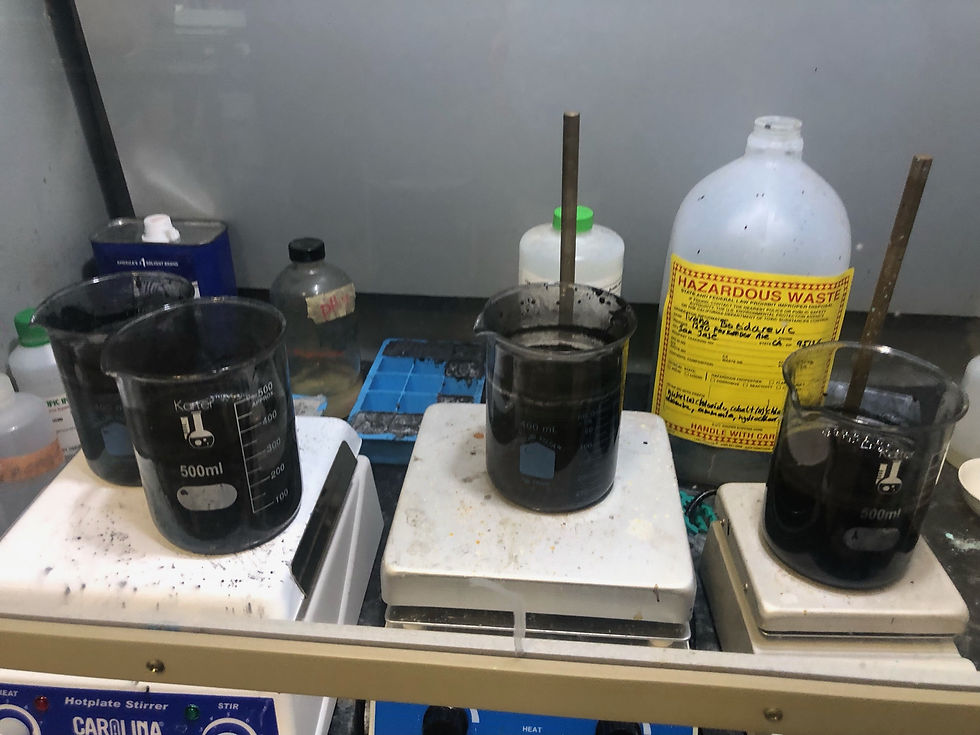
(the acid solutions with black CSA added)

(solutions being gravity-filtered)
For the alkaline concrete, we were supposed to make 16 molar NaOH, so we dissolved 115.2g of solid NaOH in water up to 180ml (don't attempt at home, highly exothermic reaction!), and ended up with this: Undissolved NaOH. Next steps unclear.

(Solid NaOH, UNDISSOLVED!)
That's all for this week, results soon!
Max Polosky
Coconut Fact #5: "Unlike some other plants, the palm tree has neither a taproot nor root hairs, but has a fibrous root system.[23] The root system consists of an abundance of thin roots that grow outward from the plant near the surface. Only a few of the roots penetrate deep into the soil for stability." - https://en.wikipedia.org/wiki/Coconut
Comments